Mehr als 60 % des weltweiten Volumens an Haftklebeetiketten werden im Fernen Osten hergestellt, darunter solche für elektronische, medizinische und pharmazeutische Anwendungen. Dies ist der Hauptgrund, warum Panoval ausgerechnet in Vietnam gegründet wurde, auch wenn der Gesamtbesitz in Europa – genauer gesagt in der Schweiz – bleibt. Obwohl man nur über einen einzigen Produktionsstandort verfügt, arbeitet das Unternehmen international mit Wiederverkäufern und Direktkunden zusammen und hat ein Geschäft mit globaler Präsenz aufgebaut. Die hohe Flexibilität in der Produktion hat es erst möglich gemacht, dass man sich heute stolz als führender Anbieter von spezialisiertem, nicht standardisiertem Etikettenmaterial bezeichnen darf. Typische Kunden sind dabei Wiederverkäufer von flexiblen Verpackungen, Etikettenverarbeiter und konventionelle Druckereien.

Panoval beschäftigt derzeit 25 Mitarbeiter und expandiert stetig. Das Management-Team besteht aus erfahrenen und international tätigen Fachleuten mit umfangreicher Erfahrung in der Entwicklung und Herstellung von Etikettenmaterial-Laminaten für die anspruchsvollsten Anwendungen. Direktor Wilco van Zwieten kam 1993 als Verkaufsleiter zu Panoval und ist heute ein wichtiger Teil dieses Teams. Seine Aufgabe ist es, neue Geschäfte voranzutreiben; dabei sieht er technologischen Fortschritt und Innovation als ausschlaggebend für den eigenen Erfolg an. Er erklärt: „In einem so wettbewerbsintensiven Markt sind es die relativ kleine Größe des Unternehmens und der Betrieb von zwei sehr unterschiedlichen Beschichtungsanlagen, die uns so erfolgreich machen. Zusätzlich zu den Mainstream-Arbeiten mit höheren Volumina, die wir ausführen, ist unser Produktionsteam in der Lage, eine Vielzahl kleinerer Spezialaufträge auszuführen, wobei das Produkt manchmal drei- oder viermal pro Schicht gewechselt wird. Wir verwenden die allerneueste UV-Hotmelt-Technologie zur Unterstützung unserer gummibasierten Systeme. Diese UV-Technologie ist die einzige, die lösungsmittelbasierte Beschichtungen potenziell ersetzen kann… Vielleicht nicht sofort, aber in zehn bis fünfzehn Jahren. Um dies zu erreichen, benötigen Sie eine erstklassige UV-Härtungslösung mit allem Schnickschnack, die diese Technologie unterstützt. Und genau diese haben wir in Zusammenarbeit mit den jeweiligen Maschinenherstellern und GEW designt, so dass wir in den nächsten fünf bis zehn Jahren alle unsere Bedürfnisse abdecken können. Wir sind zukunftssicher!“
Partnerschaft mit GEW

Das von GEW in Großbritannien entwickelte und hergestellte kundenspezifische UV-Aushärtungssystem bei Panoval umfasst fünf NUVA2-Lampenköpfe, wobei die Kapazität auf insgesamt sieben Lampenköpfen erweiterbar ist, die gegen eine Kühlwalze mit einem Durchmesser von 1.000 mm auf einer Beschichtungsanlage von Sung An Machinery (SAM) montiert wurden. Die Lampen sind um die Trommel herum auf einer soliden Rahmenbaugruppe montiert, die von der Walzenbaugruppe getrennt ist und auf Schienen aus ihrer Eingriffsposition weggleitet. Dies ermöglicht den Zugang zur Rollenoberfläche und zur Unterseite der Lampenkopfbaugruppe.
Bei der Suche nach einer UV-Härtungslösung bekam van Zwieten von einem malaysischen Mitarbeiter, der vor kurzem mit GEW bei der Entwicklung und Installation eines UV-Härtungssystems für Trennbeschichtungsanwendungen zusammengearbeitet hatte, den entscheidenden Tipp. Van Zwieten erinnert sich: „Ich besuchte das malaysische Werk, um mir die Anlage aus erster Hand anzusehen, und begann dann, mit GEW zu sprechen. Zunächst vorsichtig, da wir wussten, dass wir eine komplexe, technisch ausgereifte Lösung mit einem hohen Maß an kundenspezifischer Anpassung benötigten.“ Nach und nach nahm die Dynamik zu, als er die Anforderungen von Panoval mit der GEW-Abteilung „Specialist UV“ durcharbeitete. Er stellt fest: „Wir waren von den Mitarbeitern bei GEW beeindruckt… Ihre schnelle Reaktion und die Fähigkeit, alle unsere Fragen zu beantworten, und wenn sie noch so technisch waren. Die Zusammenarbeit mit den richtigen Leuten ist entscheidend!“
Besuch in Großbritannien
Van Zwieten besuchte dann während des Systemaufbaus die Produktionsstätte von GEW in Großbritannien, was beiden Parteien die Gelegenheit bot, das System näher zu besprechen und sicherzustellen, dass es allen Anforderungen und Erwartungen gerecht wird. Hinsichtlich des Entwurfs, der Installation und der laufenden technischen Unterstützung für das System ist van Zwieten vorbehaltlos zufrieden: „Der gesamte Prozess verlief nahtlos, wir hatten keinerlei Probleme. Sollte doch einmal ein technisches Problem auftreten, steht uns die Fernüberwachung der GEW zur Seite – aber wir haben wirklich gute Erfahrungen mit diesem System gemacht.“ Er fährt fort: „Bislang besteht der einzige Kontakt mit dem Fernüberwachungsdienst aus den wöchentlichen Berichtem, die wir automatisch erhalten und die uns nützliche Managementinformationen wie Laufzeit, Lampenstunden, Energieverbrauch und Effizienz zeigen. Das gibt uns auch Sicherheit, weil wir wissen, dass ein Problem, sollte es auftreten, sofort von der Überwachungsplattform angezeigt wird.“

Wie van Zwieten betont, wurden bei der Spezifikation des neuen UV-Härtesystems keine Kosten und Mühen gescheut, um sicherzustellen, dass es auch in den kommenden Jahren allen Anforderungen gerecht wird. „Ein typischer Laminierbetrieb installiert eine oder zwei Lampenstationen und ist dann zufrieden. Wir haben hier deutlich mehr gemacht und eine Serie von fünf Lampen hintereinander installiert, was bedeutet, dass wir den Abstand zwischen Chemikalienauftrag und Aushärtung von einem Auftrag zum nächsten verändern können, so dass wir viele verschiedene Märkte bedienen können, die bisher mit dieser Technologie noch nicht versorgt werden konnten. Aus diesem Grund haben wir uns für die Zusammenarbeit mit GEW entschieden, denn sie verfügen über das technische Know-how und die Erfahrung, die für ein so komplexes System notwendig ist.“
Einsatz in der Pharma- und Elektroindustrie
Die Zielmärkte von Panoval sind die Pharma- und Elektronikindustrie, die ein saubereres Etikett mit geringeren Restausgasungseigenschaften benötigen. Van Zwieten erklärt: „Restausgasung bedeutet, dass ein Produkt nach der Produktion weiterhin Gase abgibt; und dies kann für die Hersteller ein ernsthaftes Problem darstellen. In der Welt der Elektronik zum Beispiel kann Ausgasung zu elektronischem Versagen führen, und wenn Sie teure Artikel wie optische Laufwerke herstellen, dann muss jeder Fehlerfaktor auf ein absolutes Minimum reduziert werden, wenn er nicht vollständig beseitigt werden kann.“ Er fährt fort: „Hier macht unser UV-Härtungssystem einen wirklichen Unterschied. Wir haben unseren Härtungsprozess in unserer ISO-6-Reinraum-Produktionsumgebung erprobt und getestet, und wir können Laminate mit viel, viel geringeren Ausgasungseigenschaften herstellen. Dadurch sind wir in der Lage, diesen spezialisierten Herstellern und ihren Convertern ein saubereres und weitaus besseres Produkt anzubieten.“

Mit dem maßgeschneiderten UV-System, das speziell für Panoval entwickelt wurde, lässt sich der Abstand zwischen den Beschichtungsköpfen und den Härtungslampen präzise steuern. Dadurch kann die optimale Belichtung für eine Vielzahl von unterschiedlichen Anwendungen erreicht werden. Darüber hinaus wurde das UV-System mit sieben Lampenkopfgehäusen und fünf repositionierbaren Lampenkassetten konstruiert, was bedeutet, dass die Lampenköpfe in verschiedene Positionen gebracht werden können, um die Verweilzeit effektiv zu steuern. Durch die Verlängerung der Zeit zwischen dem Aufbringen der Chemikalien auf das Substrat und dem Punkt, an dem diese Chemikalien ausgehärtet werden, steht vor der Laminierung mehr Zeit für das Entweichen unerwünschter Gase zur Verfügung. Dies wirkt sich auch auf die Geschwindigkeit aus, mit der die Maschine laufen kann; die längere Ausgasungszeit ermöglicht eine effektive und sichere Aushärtung bei bis zu 50 % höheren Laufgeschwindigkeiten. Dazu van Zwieten: „Dies verschafft uns einen enormen Wettbewerbsvorteil gegenüber vielen US-amerikanischen und europäischen Unternehmen, die sich darauf beschränken, mit langsameren Geschwindigkeiten zu laufen.“
Messung und Verifizierung
Darüber hinaus hat Panoval auch in fünf GEW-Mehrpunkt-UV-Überwachungssensoren (mUVm) investiert, die an jedem der UV-Lampenköpfe angebracht und mit ihrem ERP-System verbunden sind. Diese können an der zentralen Position der Lampe und an den äußersten Rändern einer 500 mm Bahn und einer 1050 mm Bahn messen. Zusätzlich zu den Partikelmesswerten, die das Ausgasungsniveau unmittelbar nach der Aushärtung genau messen, ermöglicht mUVm dem Produktionsteam die Messung und Verifizierung, dass während des gesamten Produktionslaufs die richtige UV-Dosis und Intensität abgegeben wurde. Mit mUVm ist es möglich, ein UV-Härtungszertifikat für jede Charge zu erstellen, indem die Live-UV-Leistungen für jede Lampe aufgezeichnet werden. UV-Ausgabedaten in Echtzeit werden über eine RESTful API-Schnittstelle exportiert.
Das Team von Wilco van Zwieten musste einige technische Schwierigkeiten überwinden, die durch die örtlichen Gegebenheiten in Ho-Chi-Minh-Stadt entstanden sind. Die zur Kühlung verwendeten 18.000 m³/h Frischluft werden von außerhalb des Gebäudes mit einer Umgebungstemperatur von ca. 35 °C in den Reinraum gesaugt. Deshalb setzt man auf eine zweistufige Filterung und etwa 25 Meter an zusätzlichen Einlasskanälen, um die Lufttemperatur, die Luftfeuchtigkeit und eventuelle Schmutzpartikel im Inneren zu reduzieren, bevor sie die Lampenköpfe erreicht.
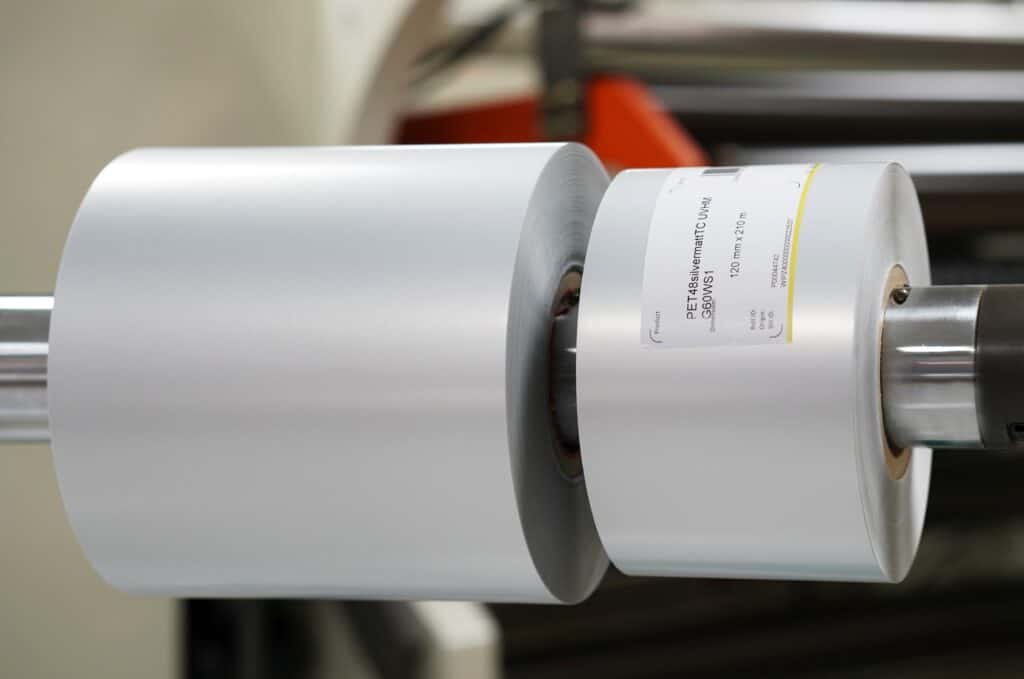
Das gesamte Produktionsteam scheint von einem starken Pioniergeist angetrieben zu werden; sein Schwerpunkt liegt auf der Nutzung von Forschung und Entwicklung zur Schaffung von Produkten, die dem Endbenutzer einen kommerziellen Vorteil bieten. Ein Beispiel dafür ist die Herstellung von Substraten für Reifenetiketten unter Verwendung eines verfeinerten UV-Hotmelt-Verfahrens. Van Zwieten erklärt: „Wir würden keinen konventionellen Heißkleber für Reifenetiketten verwenden, da er ziemlich instabil ist, insbesondere bei höheren Grammaturen. Dies führt dazu, dass der Converter die Verarbeitungsgeschwindigkeit reduzieren muss, da die Stanzmesser schnell mit Klebstoff verunreinigt werden. Stattdessen haben wir das UV-Hotmelt-Verfahren perfektioniert, mit dem wir leicht überhärten können, um einen Klebstoff mit geringer Klebrigkeit und sehr hoher Endhaftung zu erzeugen. Dies bedeutet, dass der Converter seine Etiketten viel schneller und sauberer herstellen kann. Es ist eine Win-Win-Situation für beide Seiten.“
Es sind die nachgeschalteten kommerziellen Vorteile, die Panovals UV-Produkte von den konventionellen unterscheiden und die etwas höheren Kosten der UV-basierten Rohstoffe mehr als ausgleichen. Darüber hinaus weist van Zwieten auf einen Markttrend hin, der sich ebenfalls zu seinen Gunsten auswirkt: „Immer mehr Beschichtungshersteller produzieren UV-basierte Polymere, und wir sehen, dass die Preise schnell fallen… Sie sind in den letzten drei Jahren bereits um über 40 % gesunken. Es ist nur noch eine Frage der Zeit, bis UV die Oberhand gewinnt.“
Medizinische Anwendungen
Kennzeichnungen für medizinische Anwendungen sind oft auf Vliesstoffen erforderlich, die wesentlich mehr Strahlung absorbieren als Polyester und Polypropylen. Das bedeutet, dass auch eine sehr hohe UV-Härtungsleistung regelmäßig erforderlich ist und eine Überhärtung mit bis zu 108 kW UV-Leistung auf Knopfdruck leicht erreichbar ist. Die UV-Überhärtung wird verwendet, um die wünschenswerteren Eigenschaften von lösungsmittelbasierten Klebstoffen nachzuahmen, wobei die Beschichtung so ausgehärtet wird, dass sie wenig klebrig und berührungstrocken wird, gleichzeitig aber ein hochkohäsiver Klebstoff bleibt, der extrem gut altert. Dieses Verfahren hat weitere Vorteile, wie van Zwieten erklärt: „Die Anfangsklebkraft ist gering und erlaubt sogar eine Neupositionierung, aber die Endhaftung ist sehr stark – schnell bei über 50 Newton – wie es für Hochleistungsetiketten erforderlich ist. Und so kommen wir wieder zurück zu den Vorteilen beim Converting, welches bei UV-gehärteten Lacken viel schneller abläuft.“ Sein Fazit: „Wir können alle Vorteile von lösungsmittelbasierten Beschichtungen erreichen, aber ohne die Ausgasung und die extrahierbaren Stoffe, die für die Medizin-, Luftfahrt- und Elektronikindustrie so kritisch sind.“